You’ll need to master metal detector calibration through systematic verification using NIST-certified standards and proper testing protocols. Start by ensuring proper power supply and aperture cleanliness, then position test samples correctly while monitoring environmental conditions. Regular sensitivity adjustments and thorough documentation help maintain detection accuracy and regulatory compliance. Following established calibration procedures and maintenance schedules will reveal the full potential of your metal detection system.
Key Takeaways
- Regular verification with certified metal test spheres ensures optimal sensitivity and maintains compliance with food safety standards.
- Proper setup includes checking power supply, cleaning apertures, and positioning test samples correctly in the detector’s center.
- Environmental factors must be monitored daily and documented to maintain consistent calibration accuracy and performance.
- Testing frequency should follow HACCP requirements, with results documented systematically for quality assurance and regulatory compliance.
- Systematic maintenance schedules prevent calibration drift and include inspection of components, connections, and mechanical alignment.
The Foundation of Metal Detector Calibration
While metal detectors are vital tools in quality control and safety inspection, their effectiveness relies on proper setup and verification rather than traditional calibration.
You’ll need to understand that sensitivity factors like product effect, aperture size, and environmental conditions directly impact your detector’s performance.
To establish a solid foundation, you’ll want to focus on verification using certified metal spheres to test sensitivity requirements.
Testing with certified metal spheres during verification ensures accurate sensitivity levels and reliable metal detection performance.
This process isn’t about calibrating in the conventional sense – it’s about setting your detector to ignore product effect while maintaining ideal detection capabilities.
Understanding the distinction between calibration and verification is important, as it’ll help you maintain compliance with food safety regulations and HACCP requirements.
Remember that changes in products or environmental conditions will require re-verification to guarantee consistent performance.
In addition to technical adjustments, respecting property rights is essential when conducting metal detecting activities to ensure legal and ethical compliance.
Essential Equipment and Standards
You’ll need specific tools to properly calibrate your metal detector, including NIST-certified master standards, test rods of various sizes, and documentation equipment for recording results. Your calibration process must align with established certifications like ISO 17025 and GFSI standards, which guarantee accuracy and compliance across different industries. Following manufacturer guidelines, you’ll use these tools and standards to verify detector performance through systematic testing procedures that meet regulatory requirements. Regular recalibration ensures peak accuracy and reliability, significantly impacting overall performance.
Required Calibration Tools
To properly calibrate a metal detector, you’ll need several fundamental tools and standards that guarantee accurate performance and dependable detection.
Start with metal detector test cards and reference standards to verify sensitivity levels. You’ll also need a stable calibration stand to assure consistent positioning during testing.
Your fundamental calibration equipment should include signal generators for testing detector responses to different metal types, and reliable power supplies to maintain stable operation.
Don’t forget to check your cables and connectors for wear. Environmental control devices help maintain ideal testing conditions, while conveyor belts are essential for industrial settings requiring continuous inspection.
Keep your calibration software updated, as it’s crucial for making precise adjustments.
Document all calibration results using appropriate logging tools to maintain accurate maintenance records.
Ensure that you start with ground balancing to account for soil mineralization, as it is an essential step for maximizing the potential of the metal detector and avoiding false signals.
Certification Standards Overview
Understanding metal detector certification standards requires distinguishing between calibration and verification processes.
One of the most common calibration misconceptions is that metal detectors need traditional calibration – they don’t. Instead, you’ll need to validate their performance using certified metal spheres and proper testing protocols.
Unlike industrial scales, you won’t find international calibration standards for metal detectors. Verification importance stems from the need to meet HACCP and food safety requirements.
You’ll need to account for product effect, which can impact detection accuracy, and confirm your equipment meets essential performance criteria including detection sensitivity, interference resistance, and environmental tolerance.
Modern metal detectors feature auto-balance technology, eliminating manual calibration needs. Your verification process must be documented using data loggers and supported by appropriate test samples for compliance with regulatory frameworks.
Battlefield metal detecting involves ethical considerations such as legal compliance and historical preservation, ensuring artifacts are handled with care and reported to authorities to maintain cultural heritage.
Step-by-Step Calibration Process
You’ll need to begin your metal detector calibration by verifying power supply integrity, cleaning the aperture thoroughly, and confirming all necessary test samples are readily available. Position your certified test samples precisely in the detector’s aperture center while maintaining consistent orientation throughout the calibration sequence. After completing the automated calibration process, you must validate the detector’s performance using various certified test samples at different positions to verify accurate detection capabilities across the entire aperture. It’s also important to adjust sensitivity and discrimination settings to ensure optimal detection accuracy in various environments.
Initial Setup Requirements
Before beginning the metal detector calibration process, you’ll need to establish proper initial setup conditions that guarantee accurate results.
Start by thoroughly cleaning your detector, removing any debris that could interfere with its performance. You’ll want to verify that your device is in the correct calibration mode, typically labeled as “idle” or “standby.”
Select calibration standards that match your specific contaminant detection needs, ensuring they’re made from appropriate materials with precise, known dimensions. These initial setup essentials form the foundation for accurate calibration results.
Keep the manufacturer’s manual handy, as you’ll need it to access the calibration menu correctly. Document everything you do during setup – from cleaning to standard selection – as this creates a reliable record for future reference and compliance purposes.
Incorporate ancient navigation clues into your understanding of calibration, as historical maritime symbols and techniques can offer unique insights into precision and accuracy.
Precise Test Sample Placement
Proper test sample placement forms the cornerstone of accurate metal detector calibration. When positioning test samples, you’ll need to guarantee consistent detection by placing them through the aperture’s centerline, where sensitivity is highest.
Consider how your product’s magnetic and conductive properties can affect contamination detection, and adjust your baseline settings accordingly.
For ideal detection accuracy:
- Position your test sample at the center of the aperture, maintaining consistent height and orientation.
- Account for product effect by running clean product through first to establish proper baseline settings.
- Test with different orientations when using non-spherical samples, especially wire contaminants.
- Pay attention to signal interpretation during calibration, as familiarizing yourself with tones can enhance your ability to distinguish between different types of metal contamination.
Remember that environmental conditions and packaging materials can impact your detector’s sensitivity, so you’ll need to maintain consistent testing conditions throughout the calibration process.
Performance Verification Testing
While metal detector calibration lays the groundwork, performance verification testing confirms your system maintains its specified detection capabilities over time.
You’ll need to conduct regular tests using certified metal spheres to verify sensitivity factors across ferrous, non-ferrous, and stainless steel contaminants.
Set your testing frequency based on your HACCP requirements, typically daily, and consider environmental conditions that might affect performance.
You’re responsible for documenting each verification test, including detector settings, test results, and any adjustments made.
For enhanced reliability, integrate automated verification systems like AuditCheck to reduce human error and improve consistency.
Remember to assess product effect variations and adjust your verification protocols accordingly.
Regular maintenance of your metal detector is crucial as it prevents malfunctions and ensures the detector’s longevity and effectiveness in various conditions.
This methodical approach confirms your metal detection system consistently meets required sensitivity standards.
Common Calibration Challenges and Solutions
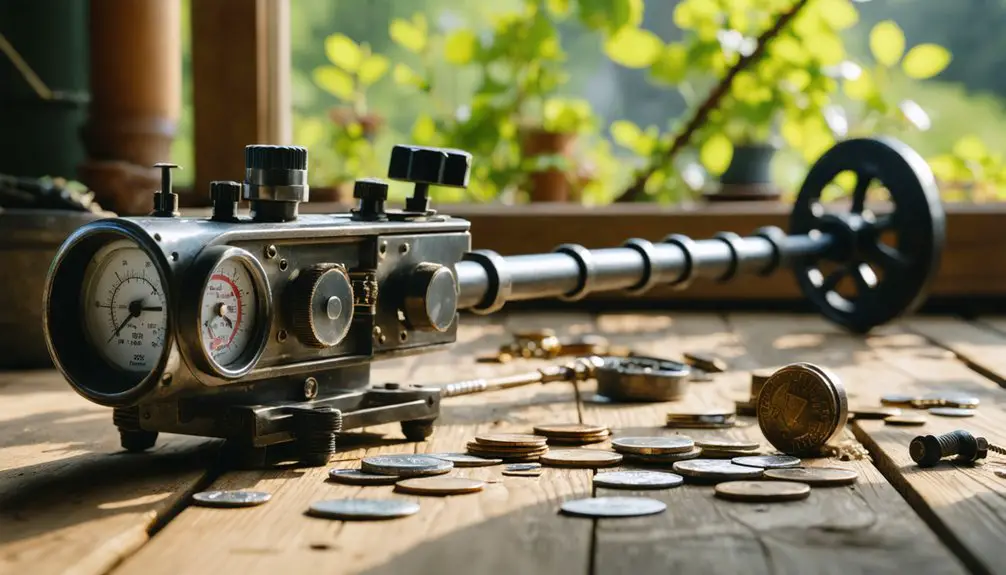
Metal detector calibration presents several common challenges that technicians must address to maintain excellent performance. You’ll encounter calibration errors ranging from software glitches to environmental interference, while sensor malfunctions can manifest through inconsistent detection responses or false alarms. To effectively tackle these challenges, focus on these critical solutions:
- Conduct regular voltage output testing to identify power supply issues before they affect calibration.
- Clean and inspect sensors routinely to prevent dust and moisture accumulation.
- Monitor environmental conditions and adjust calibration settings accordingly.
Incorporating consistent cleaning habits into your maintenance routine ensures that dust and debris do not interfere with calibration accuracy. When you notice erratic behavior or detection inconsistencies, check for loose electrical connections, damaged components, and proper mechanical alignment. Don’t forget that regular maintenance prevents calibration drift and guarantees your equipment maintains superior detection sensitivity.
Verification Methods and Documentation
Implementing a robust verification protocol guarantees your metal detector maintains peak performance and meets regulatory requirements. Your verification protocols should include daily monitoring with certified test samples and consistent procedures that follow HACCP standards.
You’ll need to coordinate with third-party auditors who’ll use certified metal spheres to challenge your detector’s sensitivity. Remember, when metal detecting, it’s crucial to adhere to all laws and regulations to avoid legal issues and ensure ethical practices.
Documentation practices must be meticulous and thorough. Track all verification tests, including dates, results, and test sample specifications.
When product changes occur, document the modifications and their impact on verification outcomes. Keep detailed records of any sensitivity adjustments or setting changes.
This systematic approach guarantees you’re always audit-ready and compliant with regulatory requirements, while maintaining the freedom to operate without interruption from compliance issues.
Best Practices for Long-Term Accuracy
To maintain consistent detection performance over time, you’ll need to implement an extensive set of best practices that address both technical and environmental factors.
Your calibration frequency should align with your operating conditions and industry standards, while accounting for temperature fluctuations, humidity levels, and electromagnetic interference.
Establish these critical protocols for peak performance:
- Monitor and document environmental factors daily, adjusting sensitivity settings when conditions change considerably.
- Implement a strict maintenance schedule that includes regular inspections of electrical components, conveyor belts, and detection systems.
- Verify calibration accuracy using standards that match your typical contaminants, positioning them precisely in the aperture’s center.
Stay ahead of potential issues by maintaining detailed records and responding promptly to any performance variations.
This proactive approach guarantees your metal detector maintains its accuracy while meeting regulatory requirements.
Troubleshooting Performance Issues
When performance issues arise with your metal detector, a systematic troubleshooting approach will help you quickly identify and resolve the root causes.
Start by checking for belt contamination, which can trigger false rejects and compromise sensitivity settings. Don’t overlook electrical noise from nearby equipment, as it’s often a hidden culprit behind erratic readings.
You’ll need to verify power supply stability and proper grounding to eliminate instrument instability. If you’re experiencing false alarms, investigate external interference sources and adjust sensitivity settings to match your product’s characteristics.
Consider environmental factors like temperature fluctuations and vibration that might affect detection accuracy. Remember to run regular verification tests using certified metal spheres, and confirm you’re following HACCP standards for compliance.
Frequently Asked Questions
Can Calibration Settings Be Transferred Between Identical Metal Detector Models?
While you might expect calibration transfer between identical metal detector models, you can’t reliably do this since product characteristics, environmental factors, and aperture variations require unique settings for each unit.
How Do Seasonal Temperature Changes Affect Metal Detector Calibration Accuracy?
Temperature fluctuations create significant calibration challenges by altering product conductivity and detector sensitivity. You’ll need to adjust your settings regularly to maintain accuracy throughout seasonal temperature variations.
What Causes Sudden Sensitivity Loss Even After Successful Calibration?
You’ll experience sudden sensitivity drops when external interference sources disrupt your detector’s field, inadequate calibration frequency allows drift, or environmental factors overwhelm your initial calibration settings.
Should Calibration Procedures Differ for Wet Versus Dry Products?
You’ll need distinct calibration procedures for each type. Run wet product calibration at lower frequencies to handle conductivity, while dry product calibration works best with higher frequencies for ideal sensitivity.
How Do Radio Frequencies From Nearby Equipment Impact Calibration Results?
You’ll need to adjust your detector’s frequency modulation when nearby equipment causes radio interference, as these signals can disrupt sensitivity levels and create false readings during calibration tests.